FMEA for Terminal Superheated Water Spray Sterilization – EU GMP Annex 1 Compliance
Objective
To identify and assess potential failure modes in a terminal superheated water spray sterilization process for large volume parenterals (LVPs) in flexible containers, using soft water, to ensure sterility assurance and compliance with EU GMP Annex 1.
Scope
This FMEA covers the entire sterilization cycle, including loading, chamber sealing, water heating, spraying, sterilization hold, cooling, draining, and unloading. It focuses on risks associated with:
- Using soft water instead of Water for Injection (WFI).
- Sterilizing flexible containers for LVPs.
- Ensuring uniform sterilization via superheated water spray, as mandated by Annex 1, Section 8.64, for routine checks on nozzles and drains.
Process Description
The terminal superheated water spray sterilization process involves:
- Loading/Unloading: Placing LVPs in flexible containers into the sterilizer chamber.
- Chamber Sealing: Ensuring an airtight seal to maintain pressure and sterility.
- Water Heating: Heating soft water to superheated temperatures for sterilization.
- Water Spraying: Spraying superheated water uniformly over the load to achieve sterilization.
- Sterilization Hold: Maintaining temperature and pressure for the required duration.
- Cooling: Cooling the load to safe handling temperatures.
- Draining: Removing water from the chamber to prevent pooling.
- Drying (if applicable): Ensuring containers are dry before unloading.
The process uses soft water, which is treated to remove calcium and magnesium ions but may contain other impurities or bioburden, unlike WFI. Flexible containers are prone to deformation or leakage under pressure or temperature variations, requiring precise control.
FMEA Table: Based on end to end process
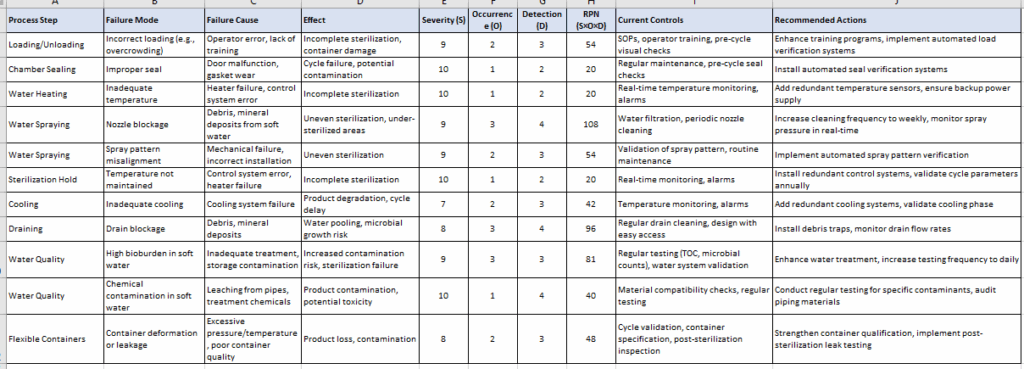
FMEA Table: Based on Nozzole blockage
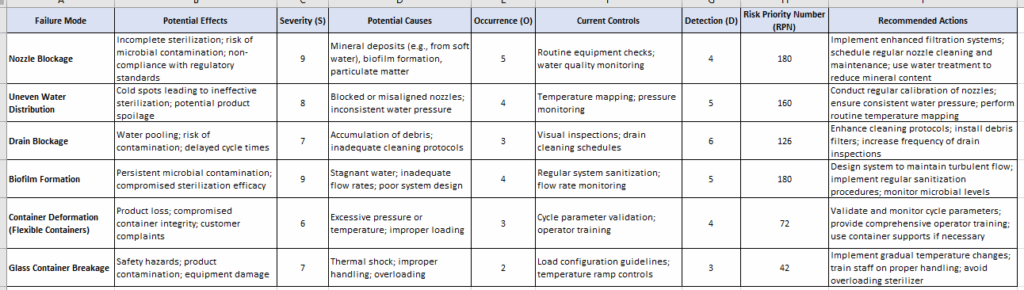
Risk Priority Number (RPN) Calculation
- Severity (S): 1 (Negligible) to 10 (Catastrophic)
- Occurrence (O): 1 (Rare) to 5 (Frequent)
- Detection (D): 1 (Certain) to 5 (Undetectable)
- RPN = S × O × D: Focus on RPN > 80 for priority actions.
Key Observations
- High-Risk Failure Modes:
- Nozzle blockage (RPN 108): Critical due to potential for uneven sterilization, exacerbated by soft water’s mineral content.
- Drain blockage (RPN 96): Poses a risk of microbial growth from water pooling, requiring robust maintenance.
- High bioburden in soft water (RPN 81): A significant concern due to the absence of WFI’s purity standards.
- Soft Water Risks: Unlike WFI, soft water may introduce bioburden or chemical impurities, necessitating stricter monitoring and treatment (Annex 1, Section 6.12).
- Flexible Container Risks: Deformation or leakage risks require precise pressure and temperature control, validated per Annex 1, Section 8.64.
- Annex 1 Compliance: Routine checks for nozzles and drains are mandated (Section 8.64). Current controls are insufficient for soft water and flexible containers, requiring enhanced measures.
Recommendations
- Water Quality Management:
- Implement daily testing for total organic carbon (TOC) and microbial counts to detect bioburden early.
- Enhance water treatment systems to minimize impurities, aligning with Annex 1’s contamination control strategy (Section 6.2).
- Spray System Maintenance:
- Increase nozzle cleaning frequency to weekly to prevent blockages from soft water deposits.
- Install real-time pressure monitoring and automated spray pattern verification to ensure uniformity.
- Drainage System Improvements:
- Install debris traps to reduce blockage risks.
- Monitor drain flow rates during cycles to detect issues early.
- Container Integrity:
- Conduct rigorous qualification of flexible containers for pressure and temperature resistance.
- Implement post-sterilization leak testing to verify container integrity.
- Validation and Training:
- Validate the entire sterilization cycle, including spray uniformity and temperature distribution, per Annex 1, Section 4.28.
- Provide comprehensive operator training on loading procedures and cycle monitoring (Annex 1, Section 7.4).
- Quality Risk Management (QRM):
- Trend environmental monitoring data (e.g., microbial counts, drain swabs) to detect excursions early (Annex 1, Section 9.5).
- Conduct regular risk assessments to update the FMEA based on process performance.
References
- EU GMP Annex 1: Manufacture of Sterile Medicinal Products, August 2022.
- ICH Q9: Quality Risk Management principles for contamination control.
- EU Annex 1 compliance for superheated water steriliser – Part 1, https://pres.net.in/2025/05/09/eu-annex-1-compliance-for-superheated-water-steriliser-part-1/
Disclaimer
This article was developed with the assistance of various artificial intelligence (AI) applications, including Claude, ChatGPT, and Grok. These tools were utilized to support drafting, editing, and language refinement. All content has been thoroughly reviewed and validated by the authors to ensure accuracy, coherence, and alignment with the intended objectives.
Additionally, high-level feedback was obtained from end users through surveys to inform the development of the concepts and control strategies presented. It is important to note that the concepts, technologies, and control strategies discussed are theoretical in nature and should not be implemented without further technical justification and comprehensive validation.
The authors accept full responsibility for the content of this article and affirm that AI tools were employed solely as assistive instruments under human oversight. No AI tool is credited as an author or contributor. This approach aligns with the ethical guidelines and policies of leading publishers, which emphasize human accountability in the use of AI-assisted technologies in scholarly works.