“There should be routine checks on the equipment to ensure that nozzles (where the water is introduced) are not blocked and drains remain free from debris“.
This technical assessment addresses the critical requirements for superheated water spray sterilization systems as specified in EU Annex 1, section 8.64. The document presents advanced engineering concepts and control strategies specifically designed to ensure that spray nozzles remain unobstructed and functional throughout sterilization cycles. By examining potential failure modes, implementing sophisticated monitoring systems, and integrating predictive maintenance technologies, manufacturers can achieve higher levels of process assurance in terminal sterilization operations.
The methodologies outlined herein represent theoretical frameworks based on industry best practices and emerging technologies, providing equipment designers and pharmaceutical manufacturers with conceptual approaches to enhance compliance. While these control strategies represent idealized solutions, they establish a foundation for practical implementation that can be adapted to specific equipment configurations and operational requirements. The integration of machine learning algorithms, automated verification systems, and specialized component designs offers potential pathways to demonstrate robust compliance with regulatory expectations for consistent sterilant delivery to all required contact points.
To ensure that water spray nozzles remain unblocked in superheated water spray sterilizers, you should implement the following comprehensive inspection and maintenance procedures:
Visual Inspection Procedures
- Regular Visual Examinations:
- Implement scheduled visual inspections of all nozzles using appropriate lighting
- Look for any visible blockages, mineral deposits, or foreign material
- Check for signs of wear, damage, or corrosion that might affect spray patterns
- Spray Pattern Verification:
- Run test cycles with empty chamber to observe spray patterns
- Look for uneven distribution or missing spray zones
- Document any abnormalities in spray coverage
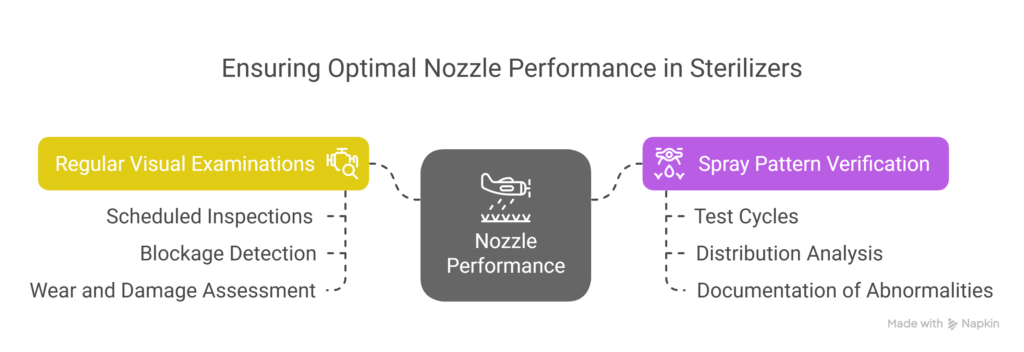
Physical Testing Methods
- Flow Rate Testing:
- Measure and record water flow rates through nozzles
- Compare against established baseline parameters
- Investigate deviations from specified flow rates
- Pressure Testing:
- Monitor pressure at nozzle heads during operation
- Verify pressure remains within specified range
- Document pressure drops that might indicate partial blockages
- Disassembly and Direct Examination:
- Periodically remove nozzles for direct examination
- Inspect internal passages for scale or debris buildup
- Clean according to manufacturer’s specifications
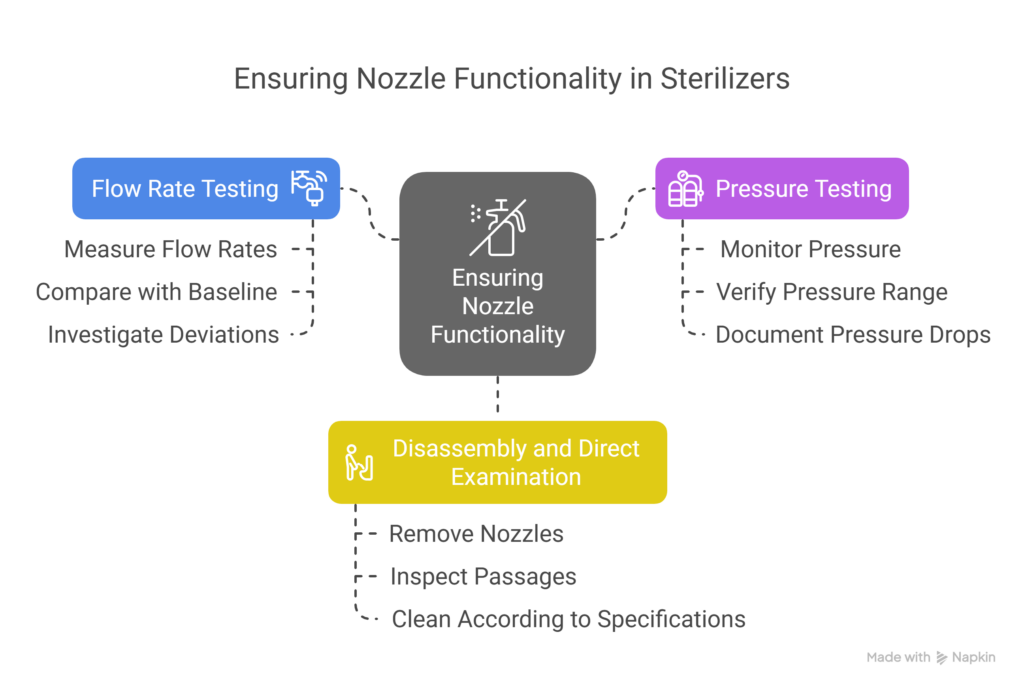
Preventive Maintenance
- Regular Cleaning Protocols:
- Establish routine nozzle cleaning frequency based on water quality and usage
- Use appropriate cleaning methods (mechanical, chemical, ultrasonic)
- Document all cleaning activities
- Water Quality Management:
- Monitor and control water quality parameters (hardness, pH, mineral content)
- Implement appropriate water treatment systems
- Consider using demineralized or purified water if feasible
- Descaling Procedures:
- Implement periodic descaling using appropriate chemicals
- Follow manufacturer recommendations for descaling agents
- Document all descaling activities
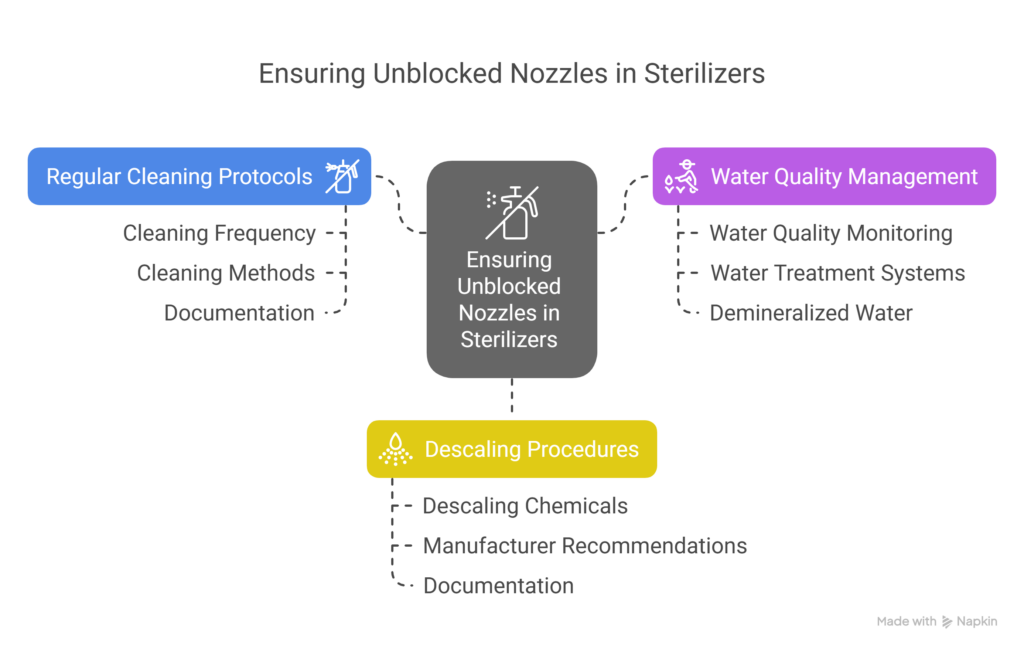
Documentation and Verification
- Maintenance Records:
- Maintain detailed logs of all nozzle inspections and maintenance
- Document any replacements or repairs
- Track trends in nozzle performance over time
- Performance Qualification:
- Conduct periodic validation studies to verify proper nozzle function
- Include spray coverage testing as part of ongoing performance qualification
- Document that sterilization efficacy is maintained
- Training:
- Ensure maintenance personnel are properly trained on nozzle inspection
- Provide clear procedures for identifying and addressing blockages
- Include troubleshooting guidelines for spray pattern issues
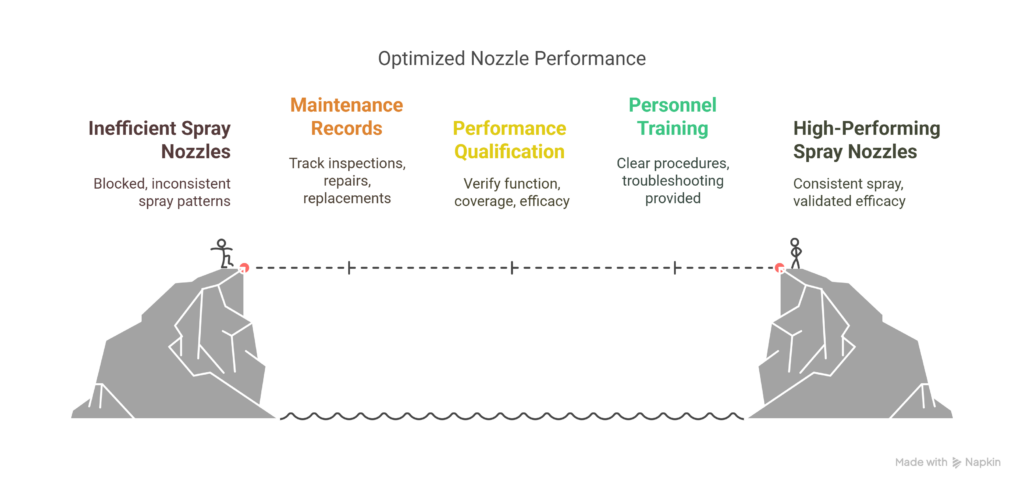
The implementation of advanced control systems for superheated water spray sterilizers requires sophisticated engineering expertise and machine learning capabilities. The methodologies outlined in this analysis provide a framework for developing high-precision monitoring and preventive measures to mitigate nozzle blockage risks. This technical assessment has been formulated to solicit feedback from equipment manufacturers with the objective of collaborative enhancement of compliance strategies for EU Annex 1 requirements. Through industry-wide cooperation, we aim to establish more robust and validated approaches to ensure consistent sterilization efficacy in pharmaceutical manufacturing environments.
Declaration
This article has been developed with the assistance of various artificial intelligence applications, including Claude. The concepts, technologies, and control strategies presented herein are theoretical in nature and require further technical justification and comprehensive validation before implementation.
Good Information